High performance, progressive and highly emotional: the Matrix LED laser headlights of the Audi e-tron GT reflect the Audi brand‘s DNA. Before the breathtaking design could be housed in the most compact installation space, the PSW developers and engineers had to crack a tough nut or two. Working in close cooperation with the Audi specialist departments, they had to overcome challenges ranging from the electronic control system, the homogeneity of the LED lights right up to the suspension and optimal integration into the wings and bumpers.
In some vehicles there’s enough installation space to fit a coffee machine. In the Audi e-tron GT there might just be room for a coffee cup.
What a technology showpiece! Bartosz Maciejewski, with a degree in mechatronics, knew right from the start that the Audi e-tron GT would be a special vehicle. From the first project plan to the homologation of the laser headlights, the PSW experts in his team had the matter in hand – and the Audi specialist departments at their side. Was the fully electric powertrain a particular challenge? “Actually not that much, even though we naturally had to prevent any electromagnetic sensitivities due to the high system voltage. Two other things were tricky for us: first, we wanted to achieve the maximum homogeneity of the LED light sources. For example, anyone who sees the daytime running lights of the Audi e-tron GT as a pedestrian or in the rear-view mirror should not see any black dots or overly bright dots in the strip lights.” And the second thing?
“We had to tuck everything away in a very small space: very high temperatures can occur in headlights, temperatures exceeding 136 °C can damage the LED lights. Here we implemented an active thermal management system with compact mini ventilation fans.” The entire process was designed in a very efficient way, including the preparation for homologation on the large 3D screen and the good coordination: “At Audi the door was always open for us, even during the night driving test – that was terrific. We are all very proud, it was a great journey for us! Then Bartosz Maciejewski laughs: “I can now recognize all makes of cars by the beams from their headlights. My girlfriend sometimes makes fun of it – but that's just how it is when you work passionately on projects like this.”
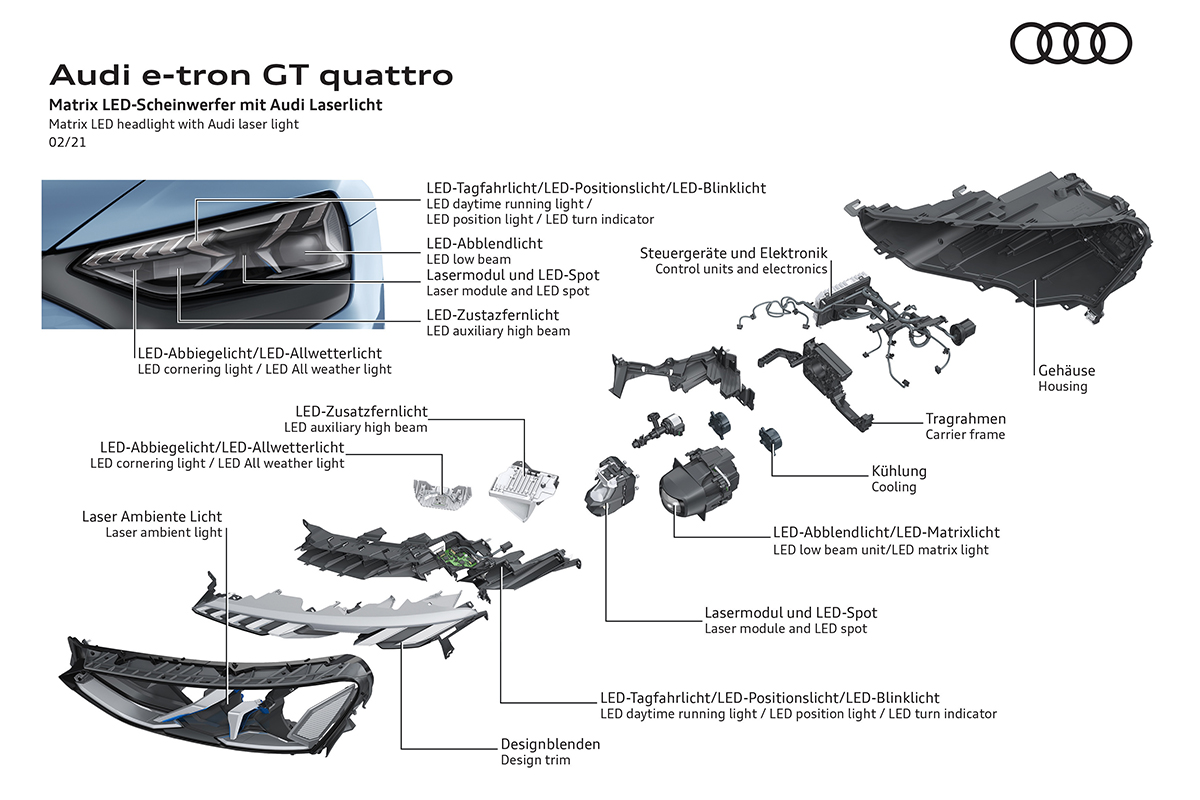
There were many new requirements in this large project – everyone in the company lent a hand.
Simulation specialist Yvonne Consten can be counted on – in the truest sense of the word. Data, simulations, numbers are her world, but she also likes exchanging ideas with her colleagues. The laser headlights were an exciting aspect of her work: “We had to check whether the headlights were fitted to the vehicle with optimal stability. To achieve this, we had to design brackets bearing a weight of more than 5 kilograms in a limited installation space. The headlights are subjected to certain frequencies: vibrations from the road and on-board equipment are simulated so that we can identify critical vibrations. It is a matter of calculating, checking and discussing our findings.” Possible damage to the headlights is relevant for insurance ratings: “Typical bumps while parking, for example, can quickly result in high costs. Crash management, driving safety, collision points, we calculate and validate all of this with low-speed crashes.”
Is there a fundamental difference between combustion engines and fully electric vehicles when it comes to such topics? “The target values are higher for combustion engines due to the additional drivetrain vibrations. The vibration characteristics of the Audi e-tron GT are completely different due to the heavy battery. We have adapted our assumptions and target values accordingly.” The reference data obtained with the Audi e-tron GT can now be used for other fully electric Audi vehicles. Meticulous work and perseverance have paid off: “My profession is all about function. And if at the same time, such a great car comes into being ...”
Interview without words: Laser headlights
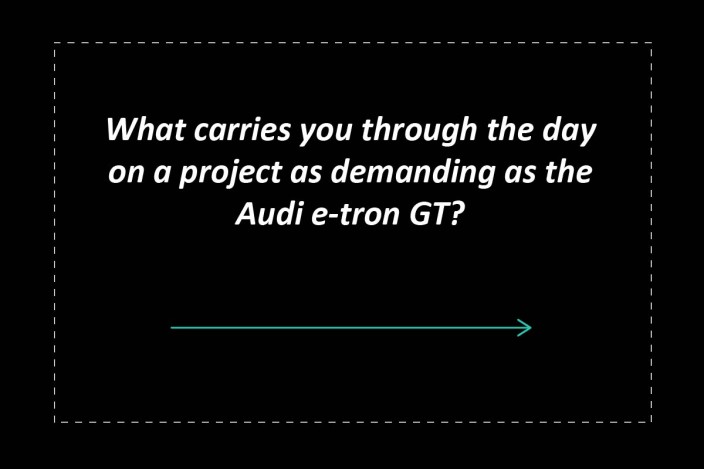
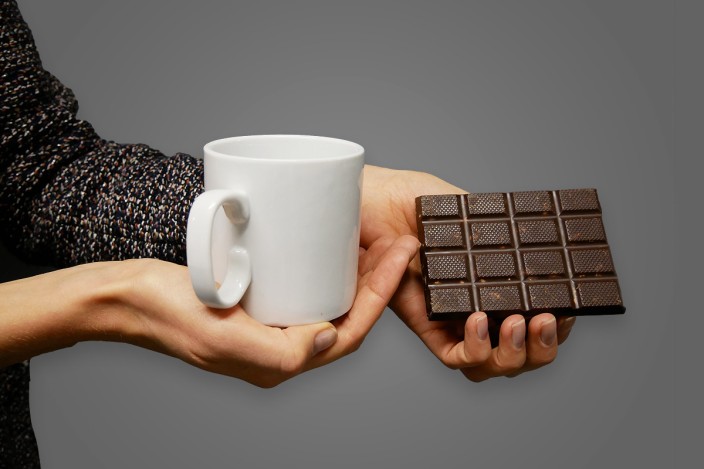
Yvonne Consten
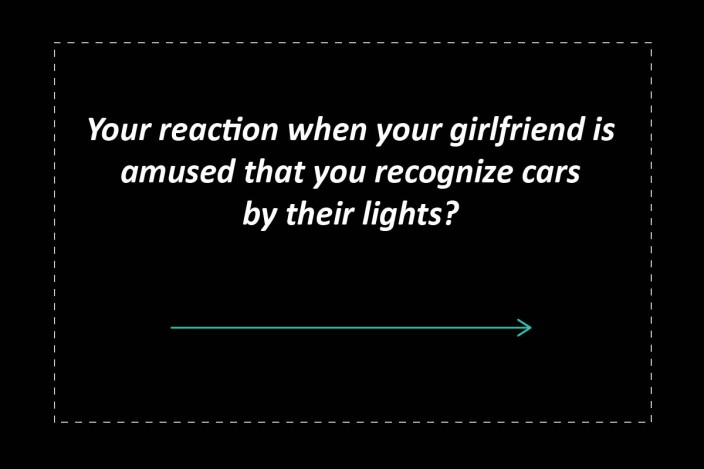
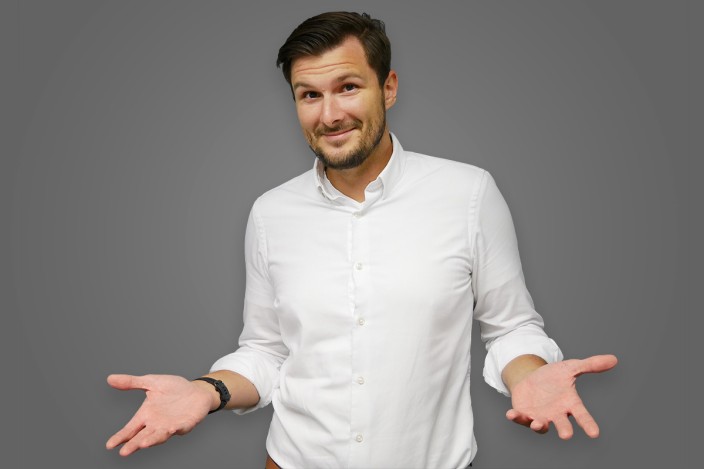
Bartosz Maciejewski
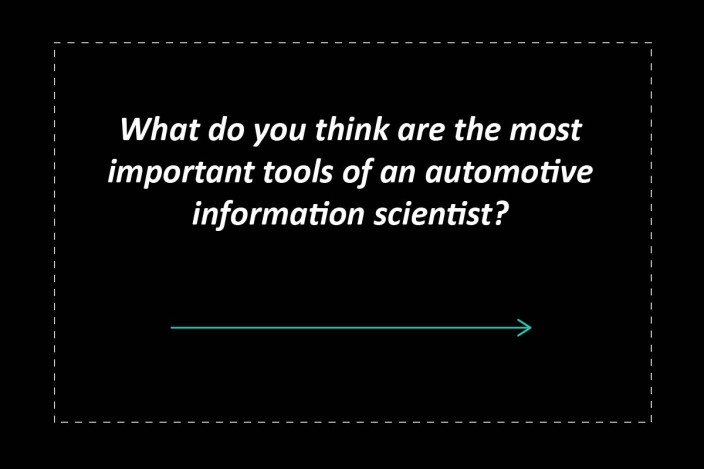
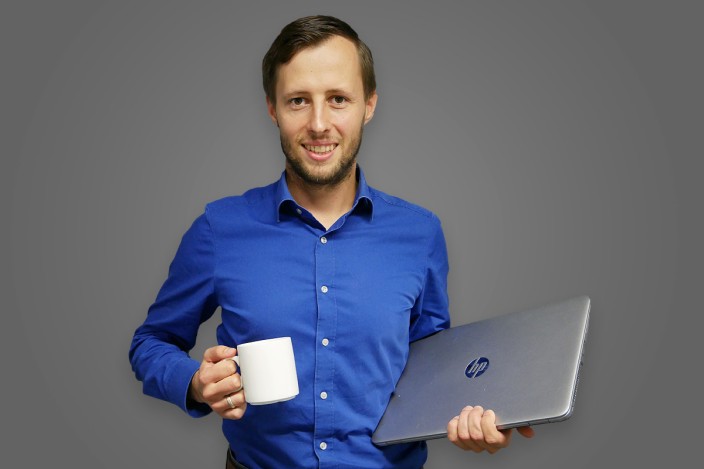
Robert Schießl
We program the vehicle-specific character, breathe life into it, and orchestrate it: Audi is the songwriter who provides the ideas – and we record them.
Data in flow: as a sub-project manager for convenience electronics for the Audi e-tron GT, Robert Schießl was involved in many topics. “Laser headlights, programming of the door control devices, seat control, boot lid control devices, air conditioning – we're actually work on nearly everything that moves and can be controlled, with the exception of the powertrain, of course. Much of what we have done, we developed from scratch.” Creating something new, getting ideas onto the road in the shortest possible time – that's what attracted the aviation and vehicle IT specialist right from the start.
“At the beginning it was a jump into the deep end. But we quickly got organised during the concept phase. What are Audi's wishes and requirements? What should the vehicle be able to do? What is the best way to realise the specifications? Together with Audi, we mastered all the challenges well. The implemented software is highly networked, so something unforeseen can always come up.”
A control unit for the convenience electronics is complex enough: in addition to the laser lights, all possible interacting functions are integrated into it, from the automatically dimming interior mirror to the roof module with user controls and ambient lighting. Was everything done on time? Schießl laughs: “We finished programming shortly before SOP, the digital world is dynamic, and so we have to react quickly to short-term certifications or new laws. What’s particularly exciting in what we do: there’s a lot of variety here. At PSW the workplace does not end at your desk, but leads through the workshops right up to the finished vehicle!”
Today a lot of the development work happens virtually, saving time and money!
“The Audi e-tron GT’s headlights were a lot of work,” says Michael Straus, in hindsight, having worked on the development of bumpers/front end for more than 20 years. “We were responsible for the technology, but of course we coordinate fitting them on the assembly line with the Audi vehicle assembly planners. For the integration of the headlights into the bumpers, we 3D-printed a special component. We had already tested it virtually beforehand, there are good tools for this. At the meeting with the Audi colleagues, we then installed it specifically on the technology demonstrator and were able to tick it off the list.” That wasn’t the only challenge, was it? The experienced master toolmaker nods: “Some things were tricky, the approval processes were also new to us – we learned a lot here.
Another field of activity is the legal requirements that we had to check, worldwide. This is essential for homologation, since every country has its own regulations. We checked this in close collaboration with the Audi experts according to the dual control principle. We’ve known each other and have worked together very well for many years – this is particularly important in such sensitive areas. Of course, there’s pressure when it comes to the tools, because this is where you are getting into millions of euros, everything really has to fit.” Michael Straus laughs: “But I rarely have a bad night’s sleep – experience helps a lot.” So, all in all, was it a smooth project? “Definitely”. When the Audi e-tron GT production got underway, the feedback from the assembly line was clear: “Everything is great!”
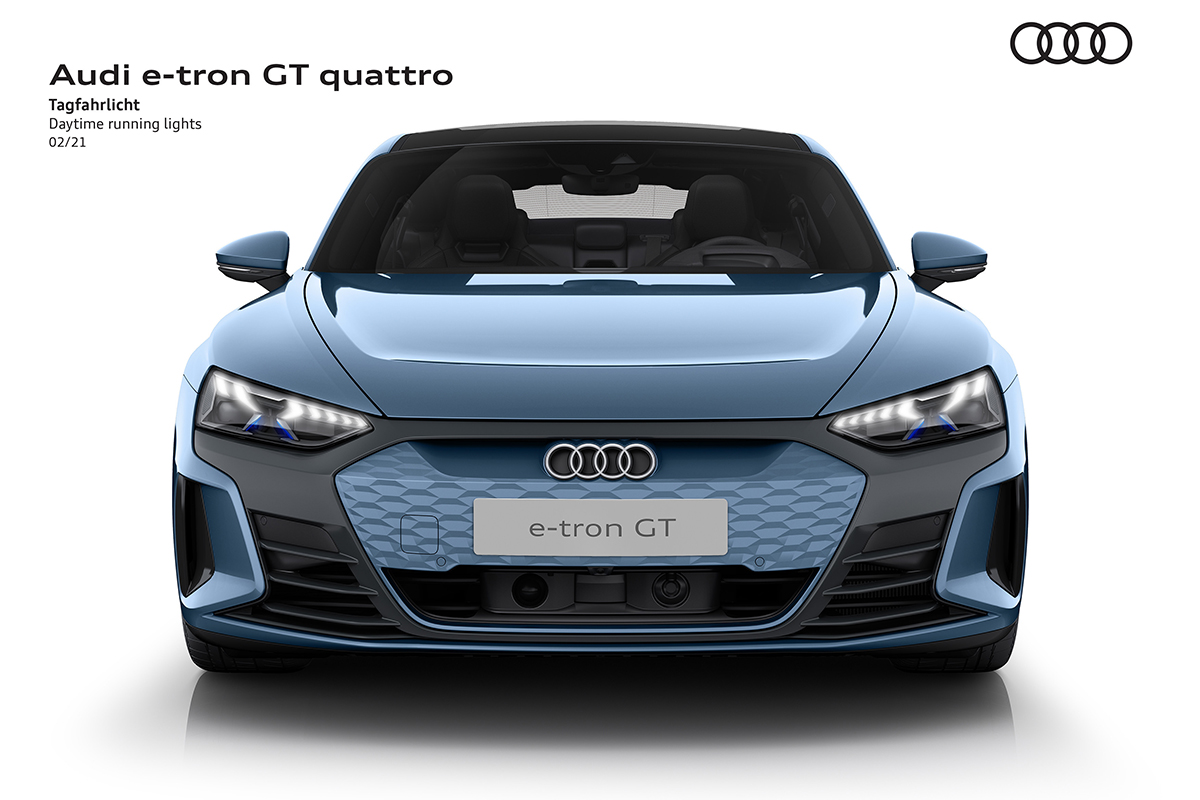
A great deal of responsibility, new processes, more interfaces: we have all made a big leap forward with this project and can be really proud!
Industrial engineer Roland Bergmann has been working at PSW for more than 15 years. Many components have already seen his desk and passed through his hands. But it was clear to him that the Audi e-tron GT’s wings would be a challenge for the team as soon as he received the first CAD data: “The Audi e-tron GT’s wings are very large, comprising five parts, with clinched and folded reinforcements. With a long tip at the front, which has to be supported. Towards the rear, leading to the door it contains an integrated air duct for enhanced aerodynamics. Under the wing there is a reinforcement and corresponding attachment points, a strut next to the headlight, which we had to provide with an additional attachment point. But the Audi colleagues presented this really well and that is why the Audi design concept held up well – we were able to implement the wing as requested.”
In addition, the installation spaces in such a sports car are very small, so often every millimetre counts. “We simulated the installation virtually with 3D glasses in advance and realised that everything would fit precisely.” And, turning to the keyword safety, what role does pedestrian protection play for the wing? “We take this very seriously. We simulate many different crash tests, from hip impacts to serious accident situations, measure acceleration and deceleration values, all of which is incorporated into the planning of the vehicle. The wing above the headlight must be designed to be elastic so that it can absorb energy. Our goal is always to achieve the optimal compromise between rigidity and flexibility.”