Aerodynamicists like Dr. Kentaro Zens also like to express these savings with the battery equivalent in euros: every meter gained can be converted directly into the costs that would have to be invested in a larger battery in order to achieve the same increase in range. Of course, Kentaro could also make a car more streamlined in a conventional way. All he needs is models, prototypes and around 1,000 hours in a wind tunnel. Alternatively, together with his team he can draw on modern open-source software and the performance of 25,000 Audi computer kernels, thereby reducing expensive test time with real hardware to just a few hundred hours.
Range is one of the most important metrics for electric vehicles. Compared to vehicles with a combustion engine, the air resistance of an electric car has a much more direct effect on its range than, for example, its weight: every 0.1% improvement a manufacturer makes to the Cd value – the measure of the aerodynamic drag of a car body – is synonymous with 800 metres of additional range.
Measuring airflow on computers
“We calculate the flow backwards, so to speak,” Kentaro explains the procedure for virtual aerodynamics development work. “How would the drag coefficient decrease if I let the air flow differently?" Starting with this question, PSW aerodynamicists use the computer to create a kind of virtual map of the vehicle surface that shows them exactly where and how the vehicle’s body has to be shaped in order to achieve the desired flow with as little turbulence as possible. The team then works its way millimetre by millimetre along the car: while many details of the vehicle front are already predetermined by brand design and the standard parts used, the radiator, for example, offers great potential for aerodynamic improvements. With a combustion engine, the air flows in a diffuse way through the engine compartment. This slows you down. In an electric vehicle, on the other hand, the air is channelled by strictly specified ducts. This has a highly beneficial effect on air resistance. The lower cooling requirements of an electric drive also means the air inlet is at times completely closed: flaps in the radiator can prevent any inflow of air and improve the vehicle's aerodynamic drag by up to ten percent.
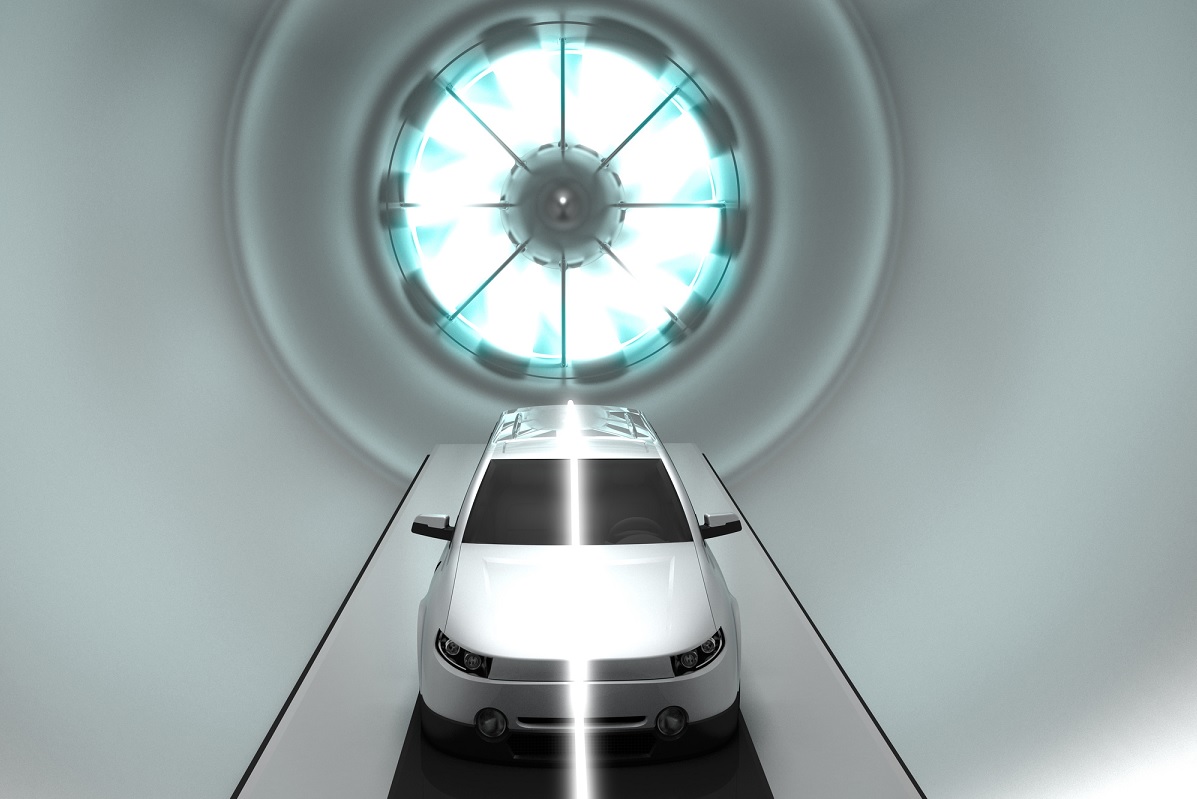
Kentaro and his team also optimise the shape of the vehicle and, above all, details such as wing mirrors and wheels through to spoilers and taillights. Even the underside of the vehicle is scrutinised by the aerodynamics specialists: without the openings typical of an internal combustion engine, an electric vehicle is much more streamlined with an almost completely smooth underbody. Every corner, every edge, every millimetre of a vehicle can affect aerodynamics and is therefore examined, challenged and, if necessary, redesigned. Kentaro always has to consider each individual modification in the overall context. It can quickly take 200 work hours to invest, for example, in improving the impact on the drag coefficient caused by an exterior mirror from a Cd value of 0.008 to 0.006. It is an interesting puzzle with many variables that the PSW aerodynamicists solve on a daily basis. Since Kentaro's work touches on many other areas of vehicle development, his department is of course extremely well networked within PSW. For the best possible result, this cross-departmental collaboration is almost as important as the extensive specialist knowledge, immense experience and, last but not least, Audi's high-performance computing cluster.
“Every car needs a body - and if you optimise it aerodynamically, you get extra range for free!”
Dr. Kentaro Zens, development of thermal management/air conditioning/aerodynamics
Complex tasks, open-source software
Probably the biggest advantage of performing aerodynamic measurements on the basis of simulations instead of the usual prototypes or 1:4 scaled models is that Kentaro can start his work very early on in the design phase. All he needs is a 3D model of the vehicle, which he and his colleagues break down into 100 million small cubes of volume before the open source software OpenFOAM calculates airflow at each nodal point. In the past, data preparation alone took two weeks – an immense amount of time that was incurred anew with every model iteration. With increasing experience and a great deal of automation, Kentaro and his team have been able to reduce the time required by more than two thirds. The dynamic development process enables tightly-scheduled revision loops and ultimately saves PSW customers a lot of time and money.
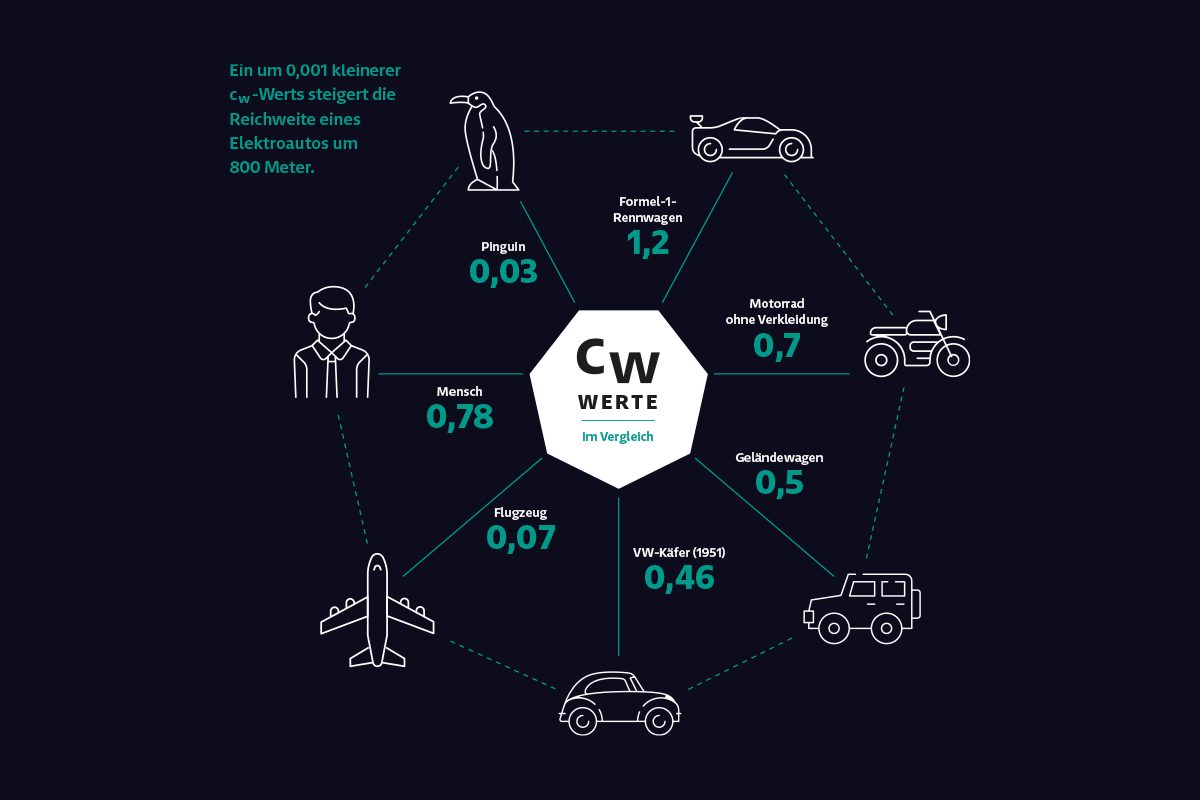
The future of vehicle development today
With the development of an upcoming electric sports car, PSW has greatly expanded its expertise in virtual aerodynamics development. The interim results and forecasts are so promising that Kentaro and his colleagues are already busy working on the future. Soon, the aeroacoustics of a vehicle – i.e. the noise generated by the airstream – will probably also be simulated and optimised with computer-aided processes.
The change in the simulation parameters from the standard test case: “wind coming directly from the front” to the much more realistic on-the-road scenario “wind coming from the side or obliquely from the front” is currently being examined in detail at PSW. Deep learning and neural networks could also play a major role in the vehicle development of tomorrow – even if Kentaro cautions of the risk that a vehicle which has been aerodynamically optimised by a computer may visually lose a lot of its character. The appearance of a vehicle must not be sacrificed at any cost for its aerodynamics. For this reason, the PSW aerodynamics department is working hand-in-hand with the designers. It is not the first time that Kentaro has sat down with a rear light designer in the wind tunnel and worked with him to perfect flow separation edges until everyone involved was satisfied with both the visual and aerodynamic result.
More than just hot air
Anyone who talks to Dr. Zens quickly senses just how passionate he is for his topic and the variety that virtual aerodynamics development work brings to his everyday professional life. In the future, he will probably spend a lot of time talking shop with designers about the perfect body lines and enthusiastically raving about the benefits of increasing aerodynamic range to PSW customers. In the end, this costs time and money – but thanks to the advanced simulations by PSW this will be significantly less than in the past.
Published in the PSW Magazine Integrated Mobility Technologies