The layperson just sees a spectacular crash – the automotive engineer sees a huge amount of immensely valuable data: how do individual components behave? Which forces act on which component connections? Do the forces reach a critical level? No matter where you are in the world: no vehicle is allowed on the road today without tests of this kind. And that’s how it has to be – because this is primarily about occupant safety. However, while it is very instructive for designers, developers and passenger safety experts to crash cars in a controlled manner, this is a very expensive part of vehicle development for the automobile manufacturer. Every crash causes costs that run into millions. A promising way of drastically reducing this expenditure is through virtual technology validation: engineers like Nijaz Dizdarevic simulate the entire process on a computer. This digitisation not only drastically cuts costs, but also speeds up the development process enormously!
A vehicle prototype equipped with countless sensors spectacularly drives head-on into a wall. The crumple zone more than lives up to its name and the crash-test dummies behind the wheel feel the full force of the airbag. The action takes place in super slow motion, watching it, we can only have a vague idea of the speed of the car.
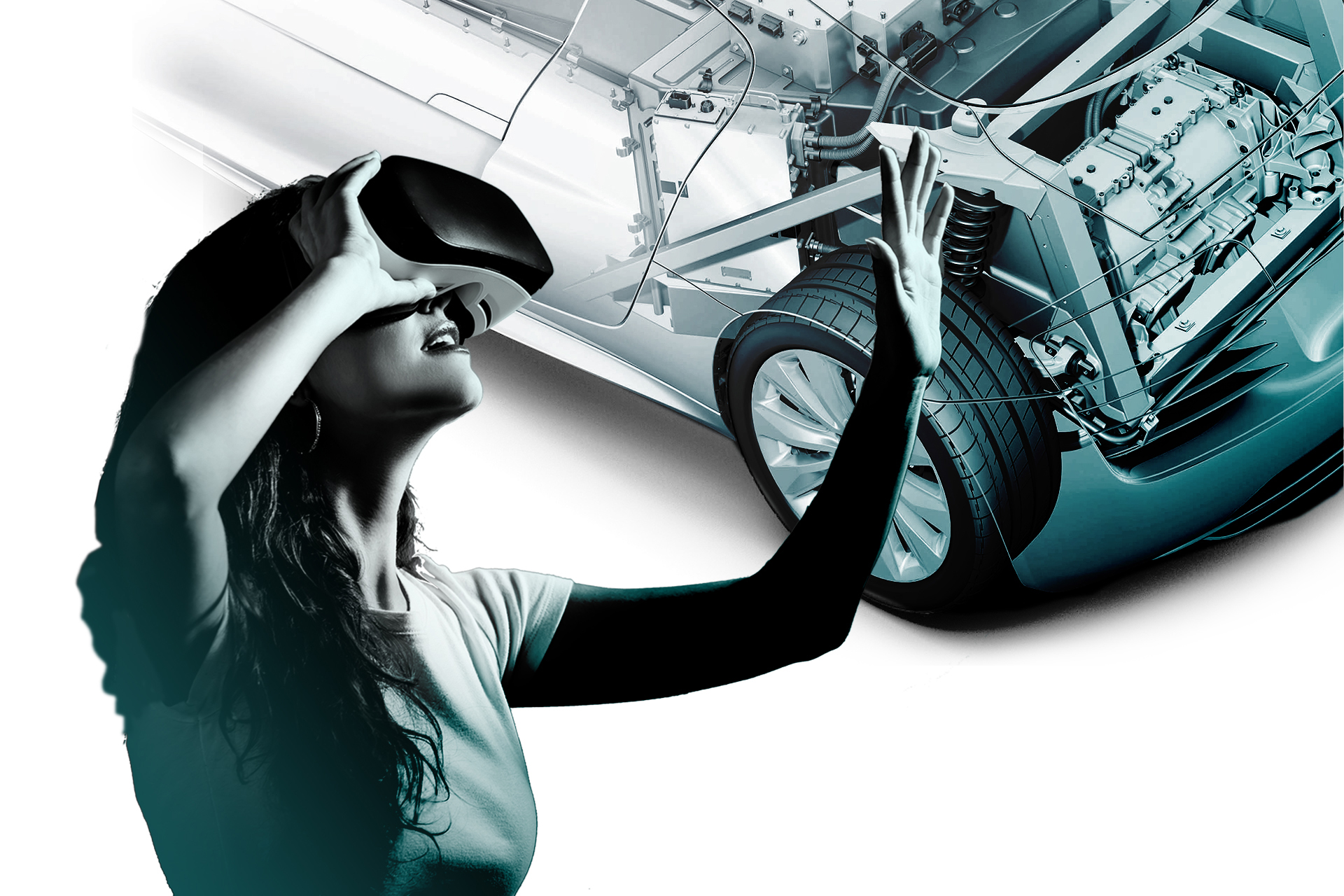
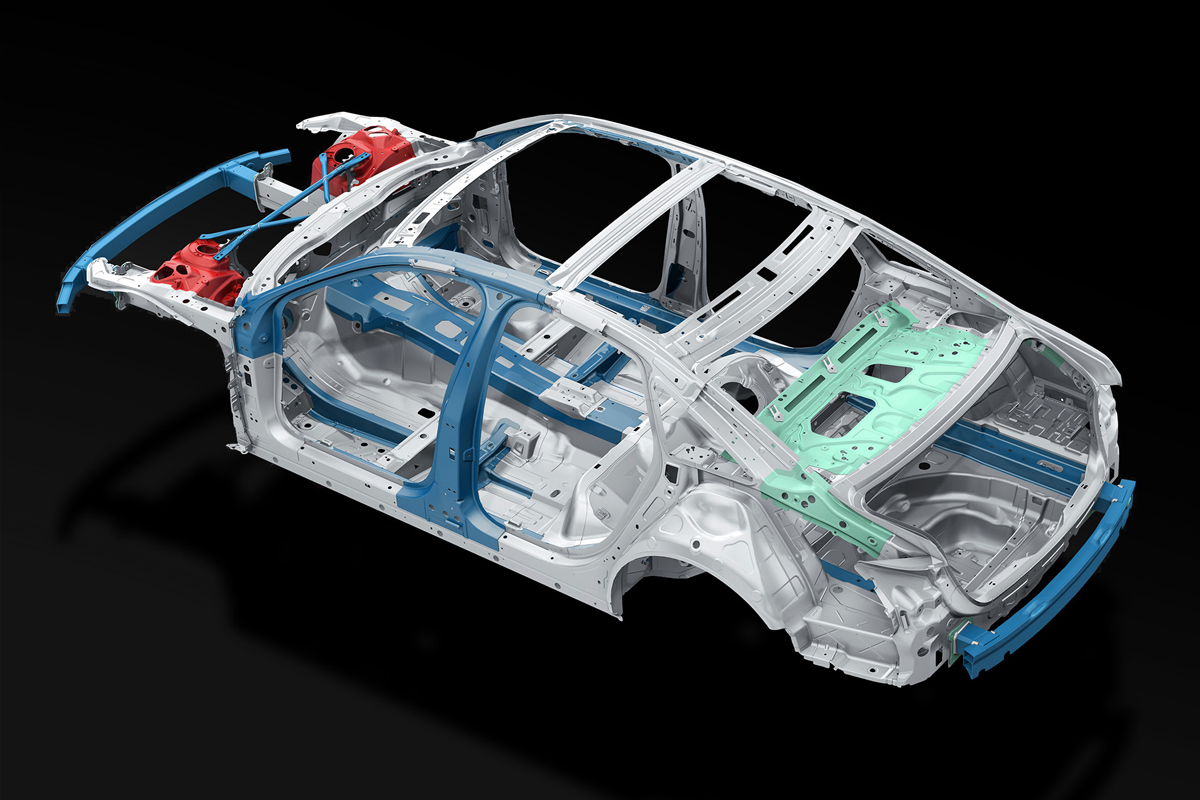
The variety of virtual crash tests
At PSW, Nijaz is responsible for the virtual technology validation of the entire vehicle body design. But what exactly does “virtual technology validation” mean? Does Nijaz sit in front of the screen all day and drive 3D models of vehicles into walls, like in a computer game? Not quite: Nijaz virtually checks every conceivable load case for each individual vehicle body component. Load cases are all possible scenarios that could later affect the vehicle body in any form in everyday traffic. By no means is this just about safety-relevant extremes such as a front-on collision – a load case can also just be "slamming the door". Even seemingly simple actions like this can measurably impair the body seal or the door itself. In the next load case, Nijaz ensures that the car headlights do not vibrate when the vehicle drives quickly over cobblestones. And so on.
A question of manufacturability
On the one hand, virtual validation contributes to vehicle safety and, on the other hand, to manufacturability. It is important to find out how virtually developed components can actually be made to plan at a later date – this is Alexander Kindsvater’s speciality. Alexander joined Nijaz’ team at the beginning of the year as an expert in manufacturing process and thermal distortion simulations. When manufacturing vehicle components, parts are often formed and bonded using pressure, heat or chemical processes. This naturally has an influence on the material itself and how it behaves later on in a load case. Above all, when coating in the cathodic dip painting (CDP) immersion bath, the suitability of newly designed body parts must be put to the test. However, that's not all: whenever a component is modified during the planning phase, Alexander again checks whether this has any knock-on effects on the materials or the systems used. This is how he himself describes his job at PSW:
“It’s like being in a kitchen – we try to measure the ingredients correctly so that we achieve the end the result we had in mind.”
Just because Alexander and Nijaz are familiar with the ingredients and the recipe, this doesn't mean that the cake will look like the pictures in the cookbook. If baking doesn’t quite turn out as expected, at the end of the day, smaller problem areas can simply be covered up with some chocolate icing. Of course, nobody makes such inaccuracies when developing vehicles: “our goal is to identify and eliminate all possible problem areas in advance, purely with virtual simulations,” sums up Nijaz, “and to achieve this at every step along the way, from design to production to functional design.” PSW maps the entire process chain virtually – thus laying the foundation for a vehicle development approach that will hopefully soon be completely free of prototypes.
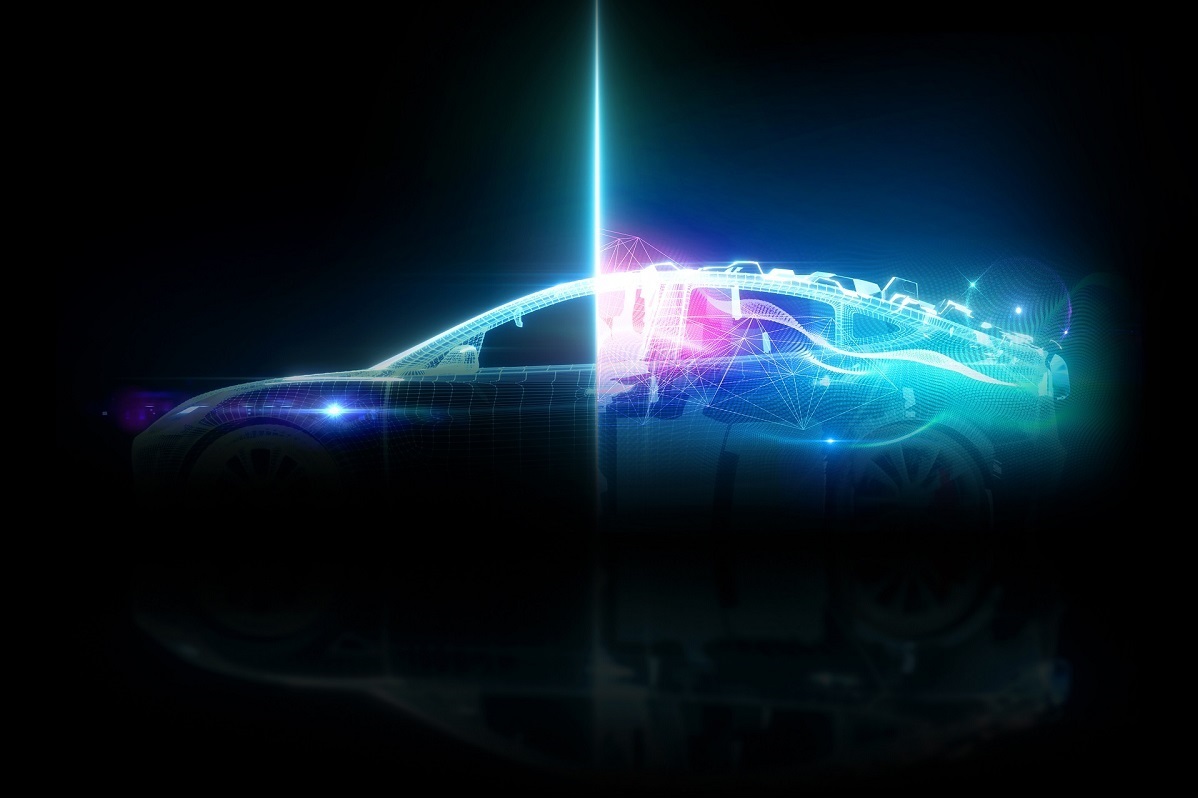
Achieving more together
Close cooperation is the key to the holistic approach at PSW. While Alexander's working routine always revolves around the question of how newly designed parts can be manufactured in the best possible way, Nijaz is continuously evaluating the functionality of the planned components. These two areas of manufacturing and functional design complement each other perfectly – with numerous interfaces to other PSW departments. A vehicle body, for example, also has to meet aerodynamic requirements and design plays a decisive role, too. Since complete vehicle models are always required for virtual crash simulations, coworkers responsible for add-on parts and vehicle safety are also regularly on board. The common denominator of all these activities: the smallest changes – for example to the functional design or manufacturing parameters – always have an affect on the big picture. That is why Nijaz and Alexander consider all components individually as well as together in component groups and in the context of the entire vehicle body. It is therefore only logical and consistent for them to carefully validate every little detail. With real hardware this would take very much longer, with their computer simulations it is only a matter of hours or days.
A quantum leap with quantum computers?
“In vehicle simulations, including absolutely everything from materials to material bonding and painting right up to the individual production steps is a relatively recent approach. Here, PSW is really doing pioneering work. As meticulously as Alexander and Nijaz proceed, the limitations of the current generation of computers are holding them back. This is a logical outcome, because the more details that are taken into account, the more complex their physical calculations become. For example, simulating a frontal collision with a fully developed virtual prototype can easily take two days of computing time, even with the high-performance computing cluster at Audi AG. For many of their tasks, the specialists make do with abstraction: instead of mapping all the parameters of each individual screw down to the last detail, they only provide some components with a few essential basic properties. Alexander has a clear comparison for this: "If we were to simulate the flight physics of a commercial aircraft, it wouldn’t matter whether coffee was being served or not.”
The balance between the level of detail and the accuracy of the results requires sure instincts, but perhaps not for long: the near future could, for example, raise the precision of simulation work to a whole new level with quantum computers. However, no matter how detailed these calculations are – there will always be room for improvement. Using state-of-the-art simulation methods, PSW virtually maps the effects of the production process chain on the material properties right through to functional design. In the validation phase, Alexander and Nijaz compare their simulated results with those of legally required prototype tests in order to identify even the slightest deviation:
“These findings are the basis for us to continuously improve our models, simulations and methods.”
Cheaper, faster, simpler
Whether Alexander and Nijaz's department is developing purely individual components or, for example, in the case of the Audi A5 Sportback, entire top hats – the so-called upper body shells fitted to a shared platform. The advantages for their customers are obvious: the simulations save them time and money. In addition, virtual technology validation reduces the complexity: by simply changing the simulation parameters, tests can be easily adapted to the regional regulations of target markets abroad. This would result in a disproportionate effort if real prototypes were used.
With an experienced team like the one at PSW, automobile manufacturers can get invaluable specialist knowledge in-house, which helps them make big steps forward towards completely virtual vehicle development. Ideally, after Nijaz’and Alexander’s have finished their work, just the load cases prescribed by law remain, which ultimately have to be tested using real vehicles. As a rule, these tests confirm what the PSW simulation experts have already virtually validated some time ago.
Published in the PSW Magazin Integrated Mobility Technologies